- By Nick Haase
- January 13, 2025
- Feature
Summary
Tech breakthroughs are keeping workers safe—and giving their employers a strategic boost.
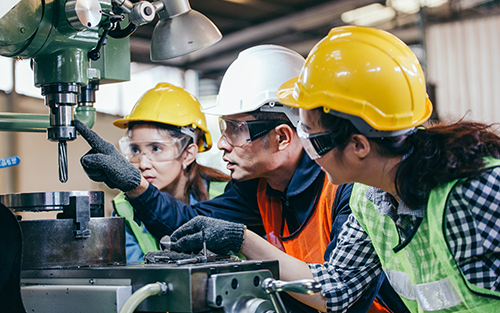
The story of factory safety is a long and winding one, from the “man-eating machines” of the industrial revolution to the Triangle shirtwaist fire and through to the modern era of ubiquitous regulations and safety inspections. Along the way, we’ve made enormous progress and made our industrial workplaces some of the safest in the world: today, thanks in part to industrial safety regulations, you’re more likely to suffer a fatal accident working in hospitality or professional services than in manufacturing.
But there’s a limit to how much can be achieved through regulations alone. To unleash the next wave of progress and make our factories and industrial facilities safer still, we’ll need to embrace not just rules and regulations, but a new generation of emerging safety technologies—including AI, automation and software tools that are already transforming so many aspects of manufacturing and industry.
Companies that lean into this process and position themselves as leaders in the emerging field of tech-enabled industrial safety, have a big opportunity. Safety shouldn’t just be about complying with the minimum safety standards set out in state and federal rulebooks. It’s also a strategic imperative, driving operational benefits across the organization.
Getting strategic about safety
Why should industrial organizations be eager to invest in safety? First and foremost, it’s easier to convince talented employees to work in safe environments. Industrial leaders need highly skilled “new-collar” workers to run their plants and operate sophisticated machinery. It simply doesn’t make business sense to put human capital at risk—literally or figuratively—by tolerating unsafe conditions.
Just as importantly, optimizing for safety makes plants more efficient and more profitable. Safety is the canary in the coal-mine for operational shortcomings: building a safer work environment unlocks new efficiencies, ensures timely maintenance and prompts organizations to streamline communications and management processes that drive enduring productivity gains.
Finally, safety supports innovation at scale. That might sound counterintuitive—we usually think of safety as requiring us to slow down, not move faster. But today’s factory floors are complex places where automation, robotics, software and advanced technologies converge in challenging ways. Prioritizing oversight and control helps organizations deploy innovations in more effective and sustainable ways, helping them capture the benefits of emerging technologies.
The power of technology
Pairing safety and innovation also leads organizations to deploy advanced technologies to augment their safety processes. In many factories, new tech is already driving safety improvements:
- Intelligent LOTO. With smart locks and sensors, connected lockout-tagout (LOTO) tools can monitor and enforce LOTO protocols, keeping machinery safely offline during maintenance. Digitizing LOTO can provide centralized visibility into which tasks are underway, with automatic alerts or shutdowns if protocols aren’t properly followed, offer digital audit trails and full documentation to support training and improvement.
- Drone inspections. Drones are revolutionizing inspections, making it easier to monitor gantries or check inventory without workers clambering to unsafe heights. In chemical factories, meanwhile, thermal imaging and gas sensors enable drones to conduct detailed safety inspections in risky environments, minimizing downtime while keeping humans out of harm’s way.
- Machine vision. People seldom notice unexpected events, and a human scanning security footage loses half their ability to spot problems within just 18 minutes. AI tools, on the other hand, never get bored or tired—and they can analyze camera footage to track workers entering restricted areas, spot safety violations, monitor PPE compliance and keep automated equipment away from humans.
- Predictive AI. Combined with IoT sensors, AI tools can predict potential problems even before they emerge. That allows teams to respond to potential hazards before they become truly dangerous, and complete repairs early and quickly, before serious harm occurs or lengthy shutdowns are needed.
Alongside such technologies, many industrial sites also use digital workplace tools to manage their portfolio of safety technologies. With a unified digital “operating system” to manage new and existing technologies and workflows, teams can track maintenance, provide alerts, streamline tasks, access documentation and ensure compliance with standard operating procedures.
That helps coordinate safety across the whole organization and breaks down the silos that have historically held back safety initiatives. Using software, safety processes can be woven through other critical functions and leadership roles—including reliability, maintenance and production—to provide strategic awareness and ensure that concerns are reported and acted upon quickly and responsively.
In a digitally ready workplace, for instance, a frontline worker no longer has to decide whether to walk away from an assigned task in order to report a problem. They simply flag a possible concern on their tablet—perhaps attaching a quick photo or video to illustrate the issue—and let someone with more seniority and experience take it from there.
When a response is needed, meanwhile, there’s no need for a flurry of phone calls, emails and radio messages to coordinate action across job functions. Everyone on the team gets automatically updated, enabling safety measures to be implemented quickly and efficiently without impacting productivity. Leaders, meanwhile, get full visibility into safety KPIs, enabling them to monitor performance and think strategically about how to improve safety—while also boosting productivity and performance.
Rewriting the rules
Safety rules are constantly evolving. In the current era of industrial innovation, worker safety is being driven not just by regulations, but also by new technologies and digital breakthroughs that add value across the organization.
That creates opportunities for industrial leaders to push beyond the minimum standards set by regulators and pioneer safety technologies that improve workplace conditions while also driving value for their business. Done right, after all, workplace safety isn’t just a set of rules. It’s a strategic priority that lets organizations support their employees, operate more intelligently and maximize productivity.
Companies that remember that have an opportunity to make tech-enabled safety a key source of competitive advantage. Joining the dots between new safety technologies and existing workflows should be a strategic imperative for industrial organizations—to keep workers safe, of course, but also to optimize operations and boost performance for the organization as a whole.
About The Author
Nick Haase is the co-founder of MaintainX, the leading maintenance and frontline work execution platform. He has spent thousands of hours on the shop floor helping businesses transform their operations with intelligent, frontline-friendly software. He regularly writes and speaks about digital transformation. He is the host of #TheWrenchFactor, a LinkedIn Live series that explores the emerging trends and technologies shaping the future of industrial operations and asset management. Follow @MaintainX to get notified when the next episode goes live.
Did you enjoy this great article?
Check out our free e-newsletters to read more great articles..
Subscribe