- November 07, 2024
- InTech Magazine
- Opinion
Summary
A trip through past issues of InTech reveals a wealth of resources for understanding closed-loop control fundamentals.
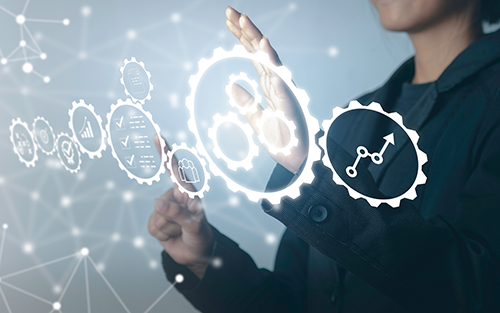
A trip through past issues of InTech reveals a wealth of resources for understanding closed-loop control fundamentals.
As I wrote in my August 2023 InTech article on temperature measurement and control fundamentals, “Automatic control in continuous processes uses industrial control systems to achieve a production level of consistency, economy and safety that could not be achieved by human manual control only. It is implemented widely in industries such as oil refining, pulp and paper manufacturing, chemical processing and power generating plants, to name a few. The “big four” process control parameters are temperature, pressure, flow and level.”
Although that article was primarily about controlling temperature, closed-loop control concepts are fundamentally the same. Only the sensors and processes are changed.
Allan Kern, PE has 35 years of industrial process automation experience and has authored dozens of papers on more practical, reliable and sustainable advanced process control solutions. Kern helps companies improve process efficiency, quality and profits on-site or with online consulting complementing in-house resources, helping bridge a skill shortage at many sites. He is the founder of APC Performance LLC.
In his February 2019 InTech article, Kern wrote, “Advanced process control (APC) refers primarily to multi-variable control. Multivariable control means adjusting multiple single-loop controllers in unison to meet constraint control and optimization objectives of an additional set of related process variables. Multivariable control is a central aspect of nearly every industrial process operation.”
While Kern’s article delves into more complex subject matter that most of our readers are familiar with, APC and multivariable control still depend on single-loop controllers. Understanding the fundamentals and/or reviewing the basics can be beneficial to technicians and operators who need a refresher.
Jim Ford’s article in June 2019 InTech describes how single-loop control is still the mainstay of advanced process control. He says, “Today, even after 50 years, APC continues to rely on the lowly flow control loop, the most basic single-loop control, as the best rejector of unmeasured disturbances and the most stable platform for the APC/optimization control hierarchy.”
Again, although Ford was writing about flow, the concepts still apply to the other three of the big four.
It starts with the sensor
Process control parameter measurements start with the sensor. The aforementioned temperature control uses thermocouples, resistance temperature detectors (RTDs), and associated transducers and transmitters. Pressure measurement requires pressure transducers, flow requires flowmeters and level requires a level measurement system. Much can be—and has been—written on each of these technologies.
A transducer converts a physical phenomenon into an electrical signal. In effect, thermocouples and RTDs are types of transducers. The use of the term is more common in flow and pressure control.
Transmitters convey a measured signal to a control device. The signal coming directly from the sensor is at a low level. The job of a transmitter is to convert the sensor output into a strong standardized signal and transmit it to a control system. Sophisticated transmitters can perform diagnostics on the sensor to determine if there is degradation of the actual element. The transmitter connects to the control system to provide the process variable (PV) measurements.
Maintaining a digital signal to the control system maximizes accuracy. Digital communications avoid the errors of converting the digital signal to analog 4-20 mA on both the transmitter end and the control system end. Digital options include HART, Modbus, Profibus and FOUNDATION Fieldbus.
Accuracy and stability are fundamental traits of any process measurement. Although closed-loop control can be accomplished in many ways with many technologies, such as programmable logic controllers (PLCs) or distributed control systems (DCSs), this article assumes a stand-alone single-loop controller (Figure 1). This theoretical controller includes a signal processing front end that converts low-level input from the sensor to a usable signal, which is compared with a setpoint (SP). The resulting output depends on the amount of error between the measured temperature, or process variable PV, and the setpoint.
Single-loop controllers are used in small facilities, or for some isolated stand-alone processes. Large continuous process facilities, such as refineries and chemical plants, use DCS to control pressure, temperature, flow and level, and how they affect the operation of the plant. In some cases and some industries, PLCs instead of—or in addition to—DCSs are used. Sometimes, PLCs control subprocesses via signals obtained from a main DCS.
PLCs have been used to control temperature for decades. It should be noted that if only temperature control is required, a DCS or a PLC is gross overkill. These systems are designed to control the entire process plants or parts of plants. Either of these devices is capable of having hundreds of control loops—temperature, flow, pressure and level.
Closing the loop
Regardless of the type of controller (PLC, DCS, or single-loop controller), the measured signal from the sensor and/or transmitter is compared to a setpoint. The resulting output depends on the amount of error between the measured temperature, or PV, and the setpoint.
In addition to accurately measuring a process, there must be a way to control the amount of correction applied to that process. The process itself “ties” the system together.
The output of the controller must have a means of actuating the controlled process. This can be heaters or burners, control valves, or positioning devices. Then the closed-loop control system begins again with the process being sensed and the controller adjusting its output.
Single-loop control gets more complicated with the introduction of proportional-integral-derivative (PID) functionality. PID is a topic for a future column.
This column originally appeared in the October 2024 issue of InTech digital magazine.
About The Author
Jack Smith is a senior contributing editor for Automation.com and InTech digital magazine, publications of ISA, the International Society of Automation. Jack is a senior member of ISA, as well as a member of IEEE. He has an AAS in Electrical/Electronic Engineering and experience in instrumentation, closed-loop control, PLCs, complex automated test systems and test system design. Jack also has more than 20 years of experience as a journalist covering process, discrete and hybrid technologies.
Did you enjoy this great article?
Check out our free e-newsletters to read more great articles..
Subscribe